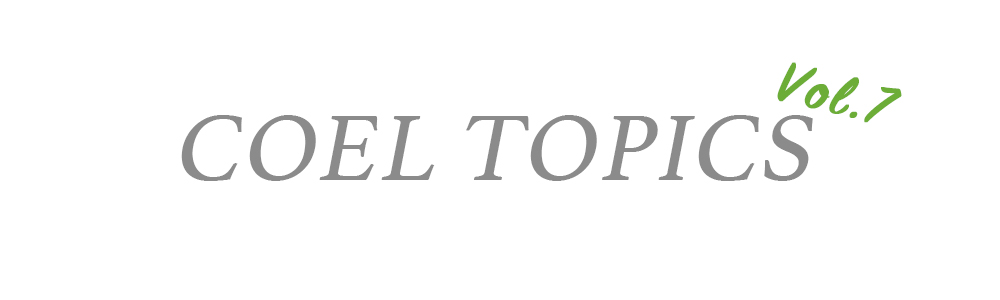
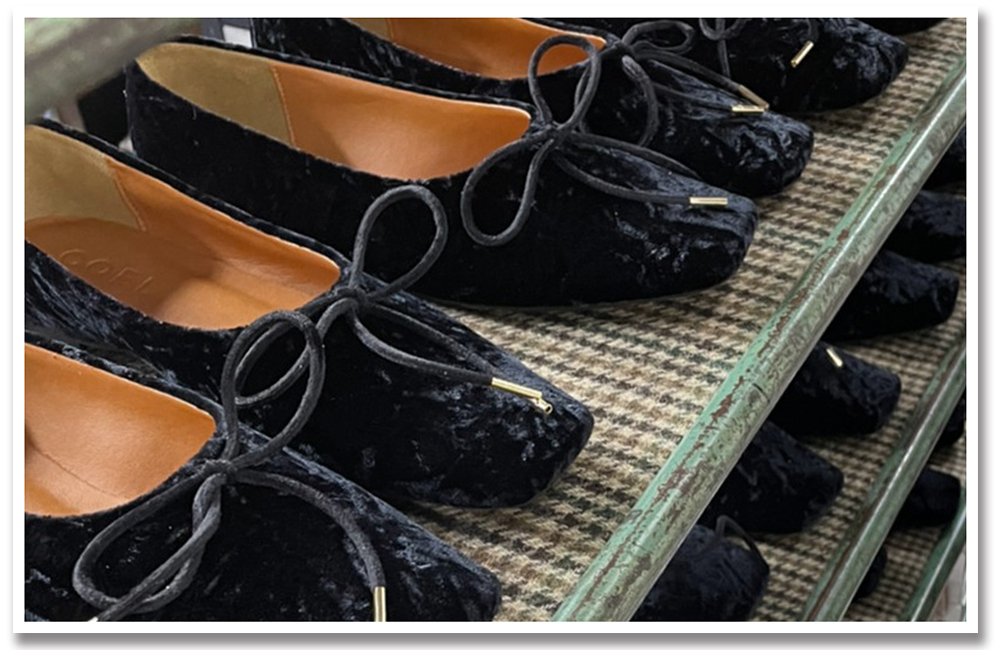
COEL工場見学
∼オリジナルシューズの製作現場をレポート!∼
∼オリジナルシューズの製作現場をレポート!∼
2021 Autumn Collection にて発売されたベロアリボンフラットシューズ。
日暮里にある「株式会社アポロ」の自社工場へお邪魔し、職人さんの技術が詰まったシューズ製作の工程を見学させていただきました!
工場では生地の裁断から仕上げ、出荷に至るまでのすべての工程を行っており、100歳近いベテラン職人の方も働く都内では珍しい工場です。
それでは一つ一つの工程をレポートいたします!
■1.裁断
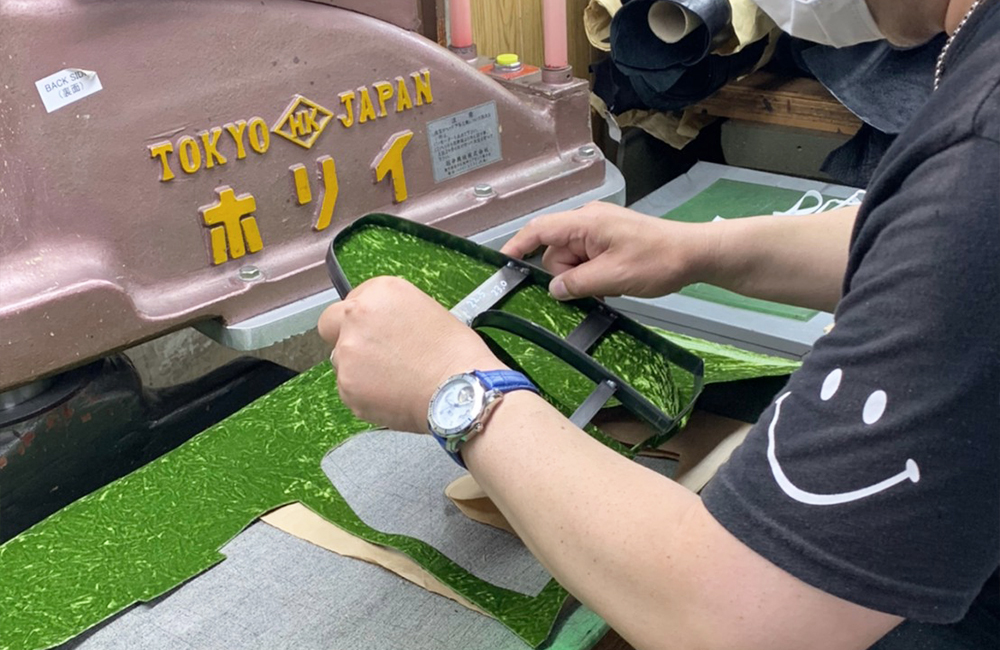
靴のデザインが決まった段階で型の製作に取り掛かり、生地を型抜きします。
今回のシューズでは発色の良さを特徴としたアセテートパイルのクラッシュベルベットを使用しました。
生地が無駄にならないように配置し、裁断機で上から圧力かけて1枚ずつ裁断します。
今回のシューズでは発色の良さを特徴としたアセテートパイルのクラッシュベルベットを使用しました。
生地が無駄にならないように配置し、裁断機で上から圧力かけて1枚ずつ裁断します。
■2.縫製
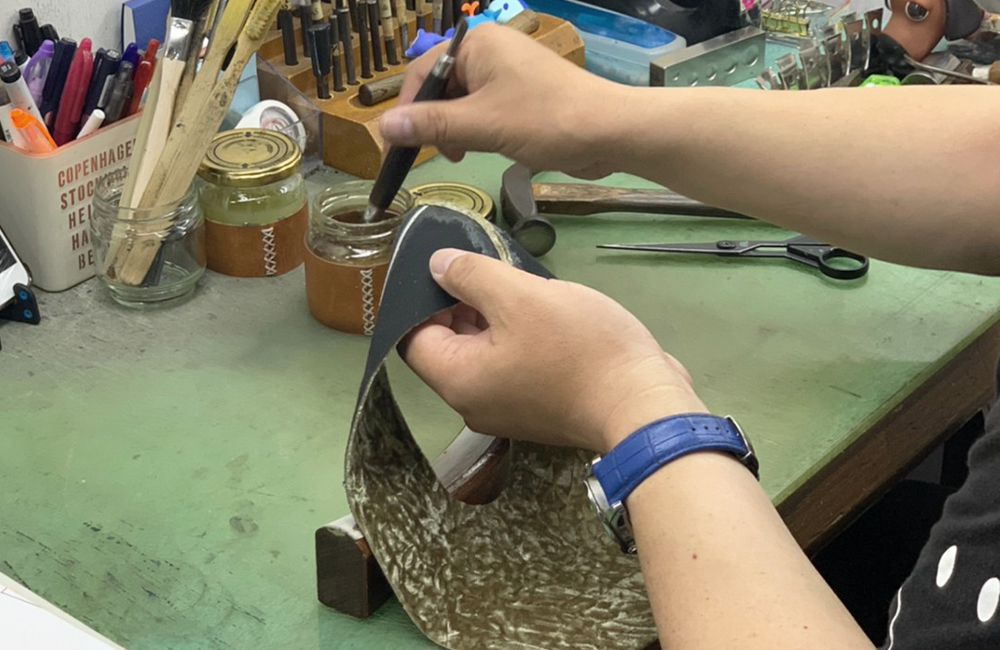
縫い目が裂けないように補強のテープをのり付けしてから、表地と裏地、かかと部分をミシンで縫い合わせていきます。
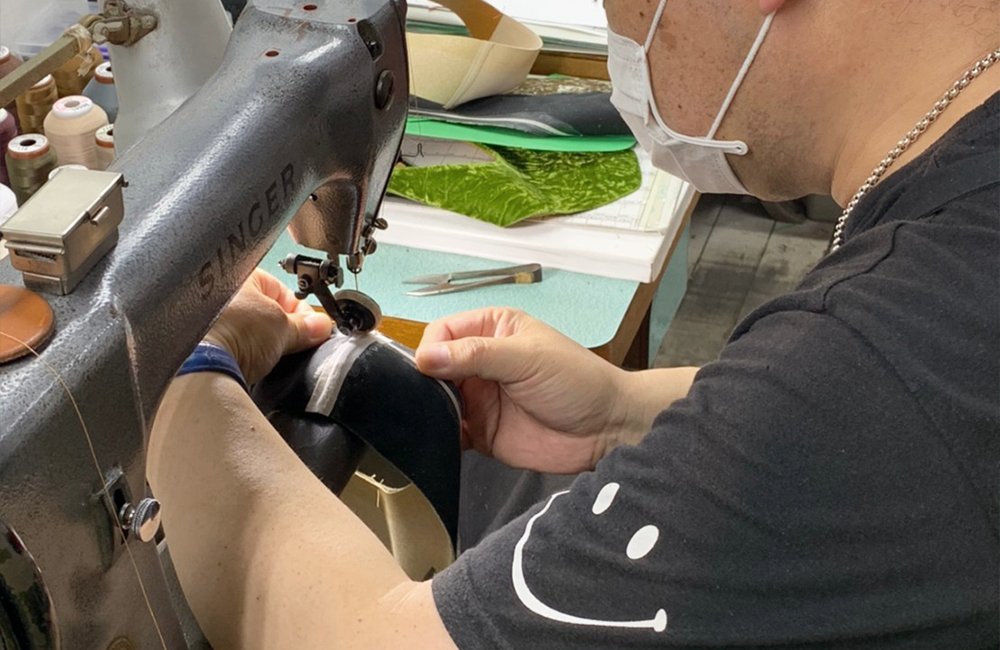
使用したベルベッドの素材は縫う際に滑りやすく、縫製が難しい生地だそうです。
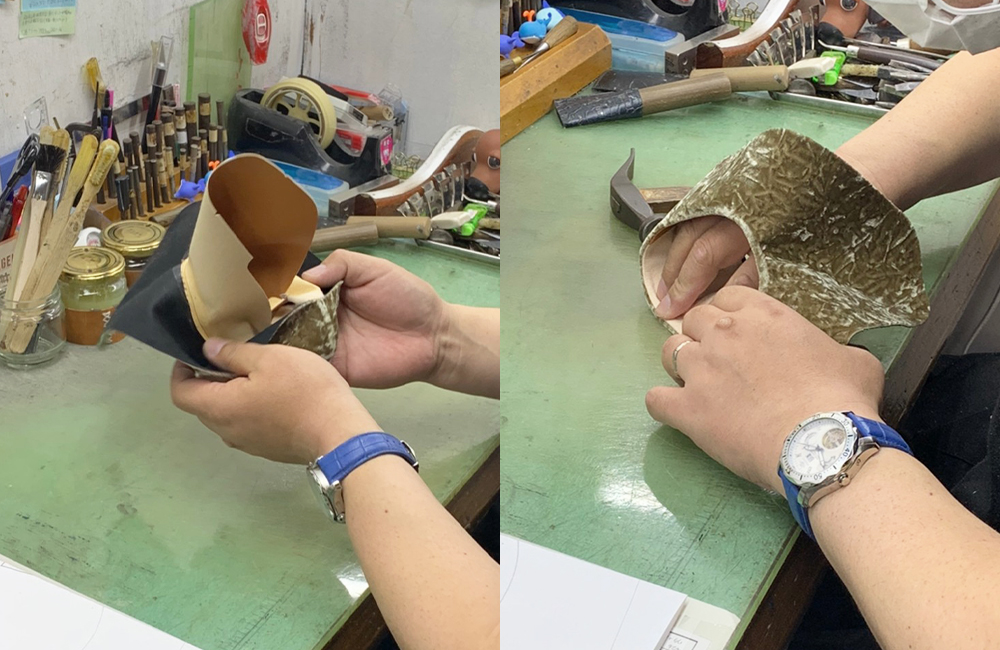
縫い合わせたものを裏返した際に、美しく見えるよう数ミリ単位で調整する技術は長年の経験を必要とします。
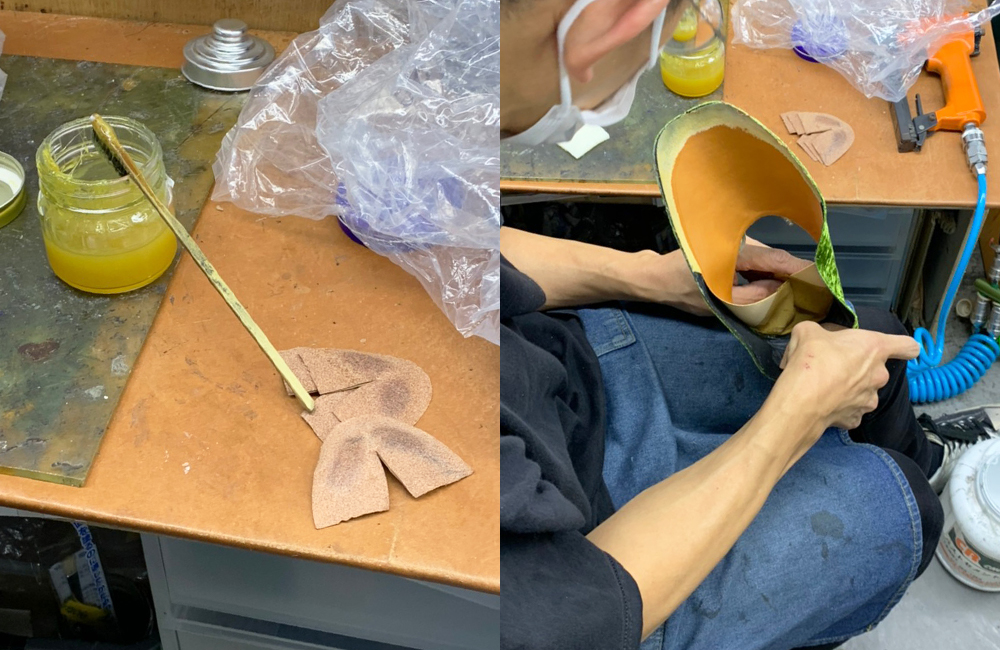
縫製が終わったらかかと部分に芯を入れます。
かかとの芯はシンナーなどを固めたものが一般的ですが、皮屑を固めたものに水分を含ませ一晩蒸らしたものを使用しています。シンナーを固めた物の方が扱いやすく簡単ですが、皮屑を固めた物の方が木型に馴染みやすく、くびれが綺麗に出るため、昔からのこのやり方を採用しており丁寧な物づくりを行っております。
かかとの芯はシンナーなどを固めたものが一般的ですが、皮屑を固めたものに水分を含ませ一晩蒸らしたものを使用しています。シンナーを固めた物の方が扱いやすく簡単ですが、皮屑を固めた物の方が木型に馴染みやすく、くびれが綺麗に出るため、昔からのこのやり方を採用しており丁寧な物づくりを行っております。
■3.吊り込み・底付け
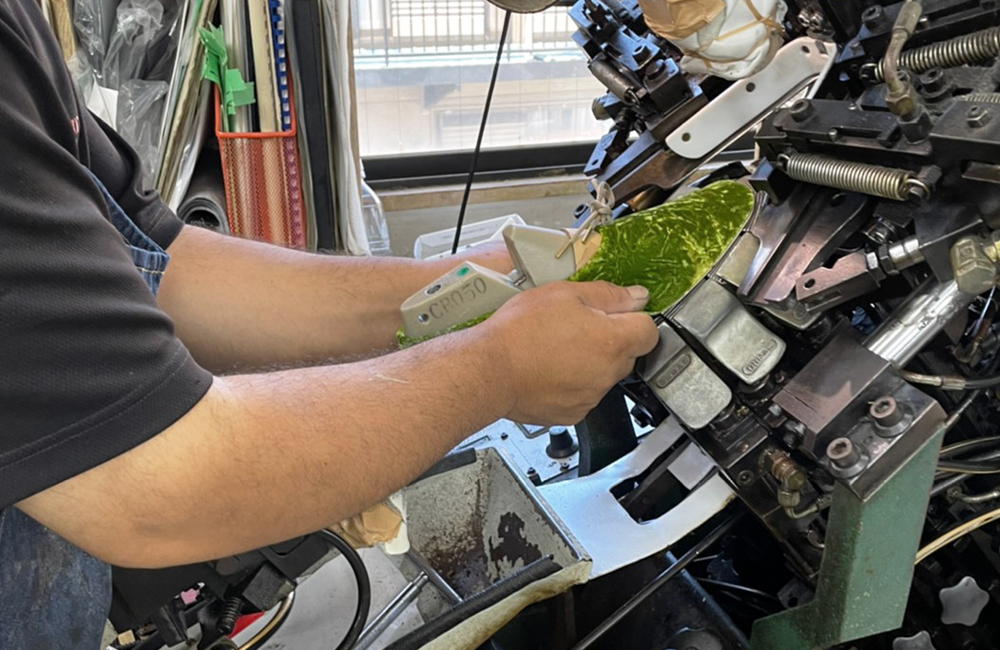
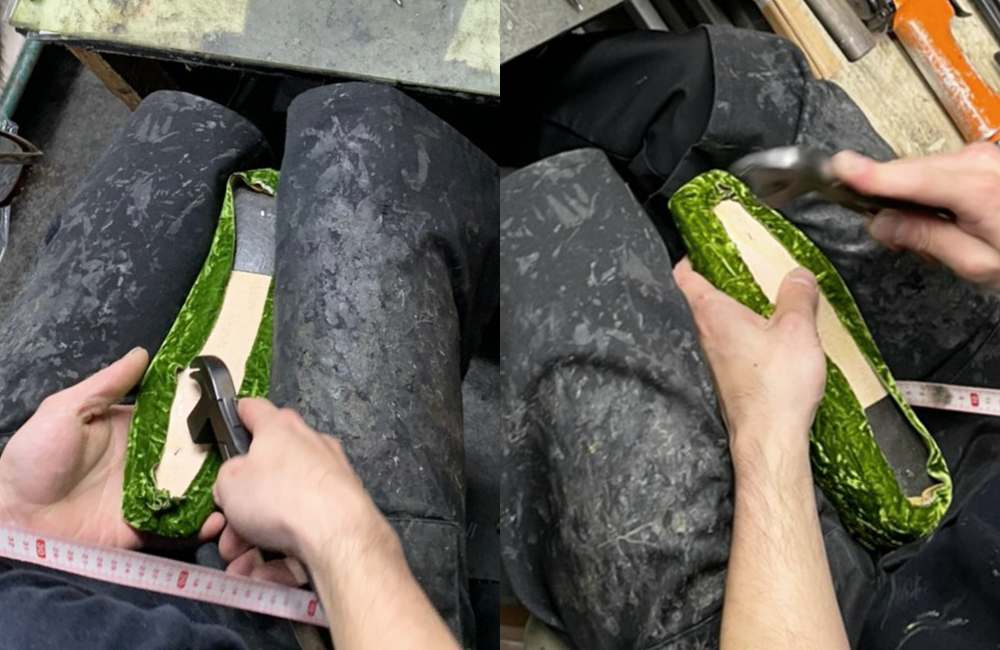
つま先の吊り込み(生地を木型に密着させる作業)を機械で行うことで効率が上がり、職人さんの負担を減らしています。機械の使用はつま先のみで他の工程は全て手作業で行っていることに驚きました。
あとは生地を引っ張りながら叩き、余分な凹凸を削って、底付けをして完了です。
慣れた手つきでどんどん仕上がっていきます。
あとは生地を引っ張りながら叩き、余分な凹凸を削って、底付けをして完了です。
慣れた手つきでどんどん仕上がっていきます。
■4.仕上げ
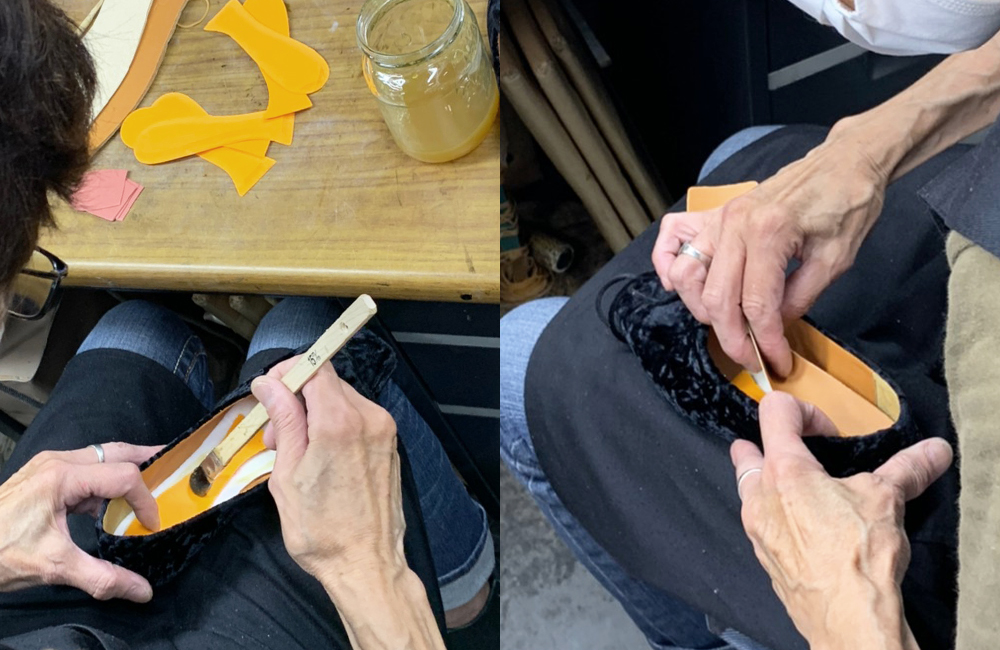
底付けをした後は、内側の細かい工程に入ります。金属突出防止の板を底に入れ、その上にクッションを貼り、のりが半乾きの状態にタイミングを合わせて中底を入れていきます。
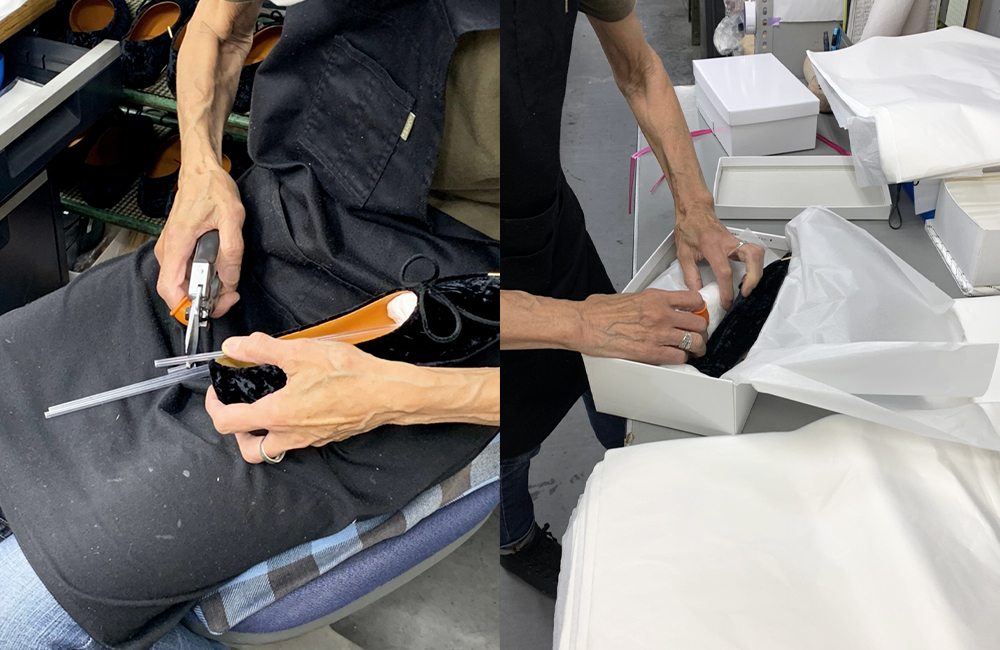
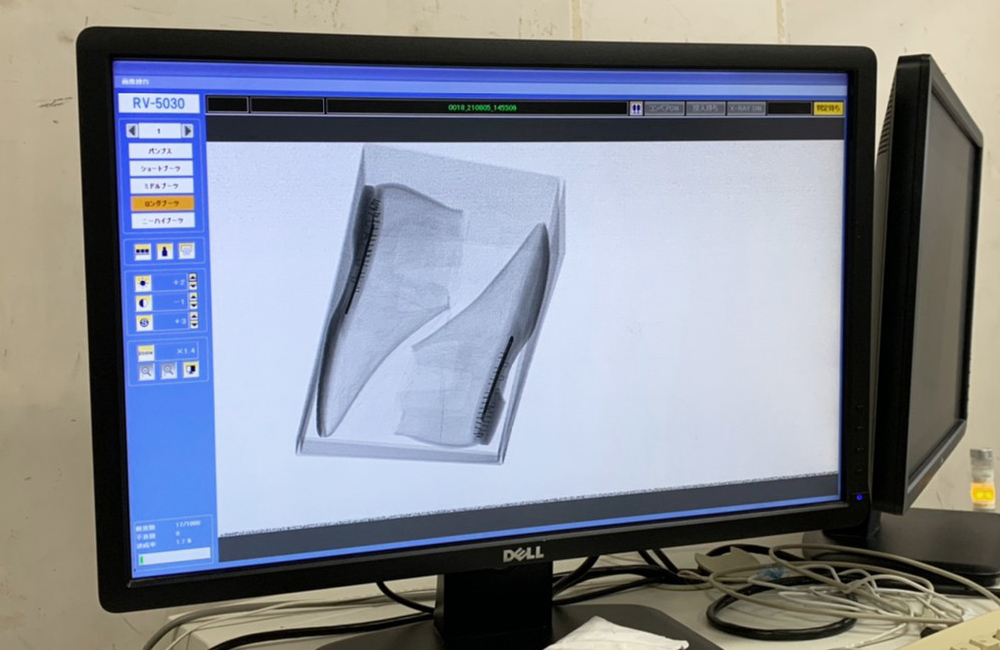
最後にリボンをすべて同じ形になるよう結び留め、表面ののりなどを綺麗に取り除きます。
形崩れを防ぐためにそれぞれの靴に合わせて詰め物を入れ、ストローをカットします。
出荷の際には箱ごと X線の検査にかけ、異物混入が無いか見逃さないように一つ一つ確認を行い、安全で確実な品質のシューズをお客様にお届けします。
形崩れを防ぐためにそれぞれの靴に合わせて詰め物を入れ、ストローをカットします。
出荷の際には箱ごと X線の検査にかけ、異物混入が無いか見逃さないように一つ一つ確認を行い、安全で確実な品質のシューズをお客様にお届けします。
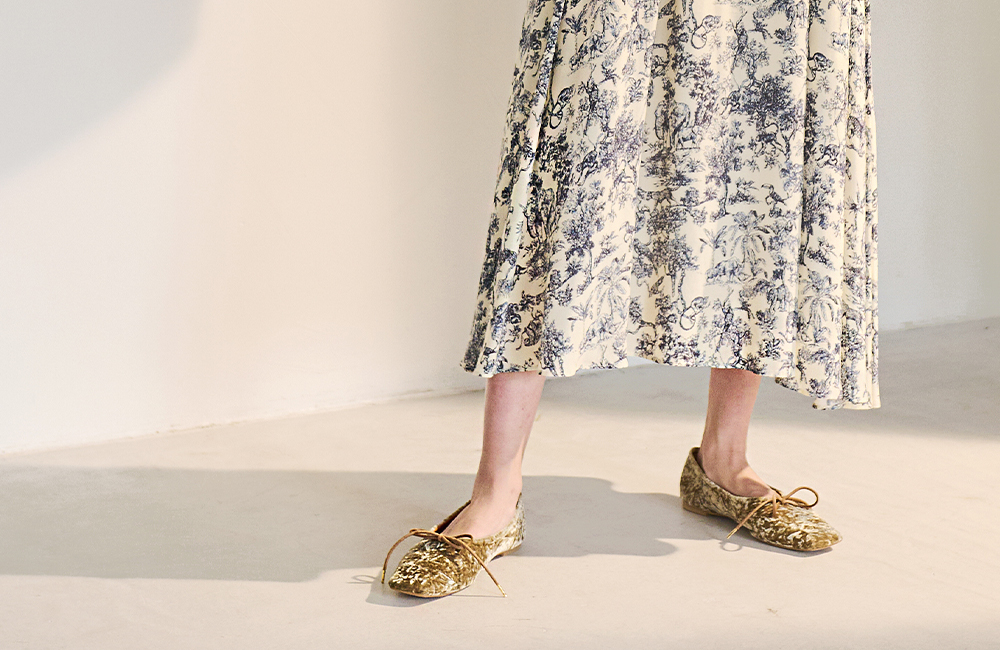
今回の工場見学で靴の制作工程がとても多いことに驚きました。
専門的な知識と、職人さんの卓越した技術がひとつの工場内で合わさり、長く心地よく愛用できるクオリティの高いシューズが生み出されているのだと感じました!
COELではこだわりのものづくりをこれからもお伝えして参ります。
ご協力いただいた株式会社アポロの皆さま、ありがとうございました!
専門的な知識と、職人さんの卓越した技術がひとつの工場内で合わさり、長く心地よく愛用できるクオリティの高いシューズが生み出されているのだと感じました!
COELではこだわりのものづくりをこれからもお伝えして参ります。
ご協力いただいた株式会社アポロの皆さま、ありがとうございました!